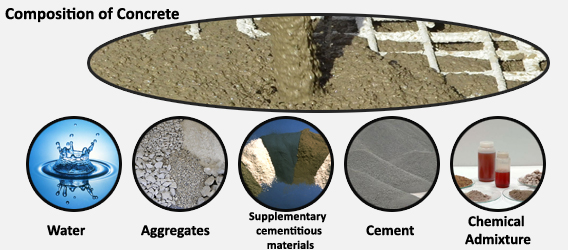 |
Composition of Concrete |
In general, foamed concretes with densities below600kg/m3 consist of cement, foam and water, with the possible addition of fly ash or limestone dust. Higher densities are achieved by adding sand. For heavier foam concrete the base mix is typically between 1:1 to3:1 filler to Portland Cement (CEM I). At higher den-sties (above 1500kg/m3) there is higher filler loading and a medium concreting sand may be used. As the density is reduced the amount of filler should also be reduced and at densities below about 600kg/m3 filler may be completely liminated. The filler size must also be reduced, first to a fine concreting or mortar sand, and then to limestone dust, pfa or ggbs at densities below about 1100kg/m3.
Cement and combinations
Portland Cement (CEM I) is normally used as he binder but other cements could be used including rapid hardening cement. A wide range of cement and combinations can also be used e.g. CEM I 30%, fly ash 60% and limestone 10%. Cement contents tend to be in the range of 300 to 400kg/m3.
Sand
Sand up to 5mm maximum particle size may be used but a higher strength is obtained using finer sands up to 2mm with 60–95% passing a 600 micron sieve.
Foam
The most commonly used foams are based on hydrolyzed proteins or synthetic surfactants. Synthetic based foaming agents have longer storage times and are easier to handle and cheaper. They also require less energy to produce foam, however protein based foaming agents have higher strength performance.
The preformed foam can be divided into two categories: wet foam and dry foam.
Wet foam has a large loose bubble structure and although stable, is not recommended for the production of foamed concretes with densities below1000kg/m3. It involves spraying a solution of the agent and water over a fine mesh, leading to a foam with bubbles sized between 2–5mm.
Dry foam is extremely stable, a characteristic that becomes increasingly important as the density of the foamed concrete reduces. It is produced by forcing a solution of foaming agent and water through restrictions whilst forcing compressed air into the mixing chamber. The resulting bubble size is smaller than wet foam at less than 1mm in diameter and of an even size.
Foaming admixtures are covered by BS 8443:2005 Specification for establishing the suitability of special concrete admixtures(BSI, 2005).
Other aggregates and materials
Coarse normal weight aggregates cannot be used in foamed concrete as they would sink in the light weight foam.
Mix details
The properties of foamed concrete are mostly dependent on the following aspects: volume of foam, cement content, filler and age.
Water/cement ratio has relatively little effect in strength but other factors like filler content and particle size do.