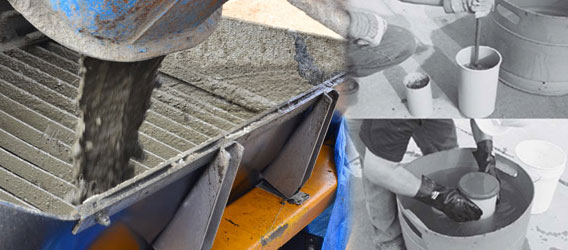 |
Material Testing and Quality Control Department
|
At Mastour Ready Mix, we understand that our concrete and cement
products, are the most unique and versatile building materials in the
world/gulf/saudi. It can assume virtually any shape and reach great
strengths. Concrete is ideal for any building project such as
residential homes, schools, high-rise buildings, bridges, dams, highways
etc. Concrete is perishable in its plastic state and very “sensitive”
from the time the raw materials are combined to the final product.
Mixing, transportation, placing, and curing can influence its plastic
and hardened properties. This is why Mastou Ready Mix places great
emphasis on quality by expanding the parameters of its concrete quality
management model from quality control to quality assurance. Mastou Ready
Mix is leading the way to higher quality practices with the
implementation of a Quality Management System based on the guidelines
and principles
Laboratory materials
Different quality tests for Ready mix concrete depending on the time of testing
Tests done before delivery: – such as the test (SLUMP TEST) by which
the test in coherence of concrete mix where to take a sample from the
truck before delivery and is measured by the degree of decline in
concrete as shown in Figure.
Tests after the mortar : – After the arrival of concrete to the
delivery location, sample was being made to make sure that it in in
compliance with the specifications required by client from 15mpa to
100mpa. , According to American standards – British – Saudi Arabia, as
well as the American Concrete Institute through cubes or cylinders which
are cured and will be tested after 7 days and 28 days, as I have a
company mobile laboratory, issued full reports and statistical analysis
to verify the specifications and mix design already installed, also
verify the quality of the concrete at the site after 7 days and 28 days
through a variety of tests conducted at the site and mention some of
them for example.
*Hammer Test.
*Test section (coring Test)
Raw materials used
The company produce ready-mixed concrete on the best materials available.
Cement
*OPC Portland cement according to the specifications of America.
*Sulfate Resistant Cement is resistant to the attack of salts, according to the specifications of America.
*Pozollan Portland Cement by American standards.
Graded gravel
basalt rock is extracted harsh clean by bombing and that is crack by
refracting a primary and secondary cracking Assistant (mill) then
Separation of materials through Screen multiple production in different
sizes (3/8”, ¾”, ½”.1” ) by
American standards.
Sand : – Sand mechanically screened to produce clean sand and free
from silt, shall be subject to laboratory tests to ensure its compliance
Specifications for the U.S. A .
Additional materials
Based on the effort required by the client and the mix design that is
prepared in our laboratories, some of which require addition of
chemical, and to mention some of them: – .Colored concrete floor for the
addition of chemical dyes, iron oxide and (IRON OXIDE) in different
colors Use (MICROSILICA) and that of the tanks, swimming pools,
concrete, marine and that what is known
(Water Proof)
Article RETARDER) so as to delay the setting time of the concrete.
Article SUPERPLASTICIZER add this article on the effort required from the client.
Materials parallel STABILIZER.
Article ( HIGH RANGE WATER REDUCER) .
Material added to the concrete used in the sea (CORROSION INHIBITOR )
There are also special specifications and special chemicals for concrete fiber and heavy weight concrete .
cooling system
company has a cooling system consists of chiller to cool the water to
8 degrees Celsius, ice plant is also available at the company’s plant,
covers factory production of ready-mixed concrete to reduce the
temperature of the concrete, especially during hot weather. (summer).
Water purification plants
The company has plants and water purification device examining the
ratio of salts (TDS ) Where the water purification process and to ensure
compliance with the U.S.A standards, is an important factor to achieve
the highest quality of concrete.
Technical recommendations
Should follow the recommendations of engineering during the casting: -
- On the client, to make every effort to unload the concrete from the
truck mixer as soon as possible, in terms of time factor is very
important for the quality of concrete.
- During the concrete pouring, especially in columns, ceilings and
cabinets recommends using vibrators to avoid honeycomb and to removed
air voids to maintain the concrete quality and shape.
- We recommend using good wood, especially for the columns in order to maintain the quality of the concrete and shape.
- We recommend that the request for additional water to the mixture at
site is prohibited, any additional water at site adversely affect the
quality of concrete.
Recommendations of the ready-mixed concrete after casting :- Moisture
must be maintained during the process of curing of concrete after
casting so as not to loss moisture rapidly as the rapid loss of moisture
during hardening will result in no doubt surface cracks. We recommend
treatment with wet burlap or work pools of water with sand barriers to
keep the water as long as possible.
Concrete recommendations to address backlog of doubt :- We recommend
that you keep the surface moist at all times and can be delayed doubt
concrete for several hours and that was the result of the chemical
additives for concrete, which in turn delayed doubt concrete for several
hours. We recommend that you deal with concrete containing Microsilica
How to Order
To learn more about Mastour ReadyMix or to place your order, Please do feel free to Contact Us